燃煤發(fā)電機組因燃煤會(huì )產(chǎn)生大量含二氧化硫煙氣,常用濕法脫硫來(lái)處理。濕法脫硫效率較高、反應速度快、脫硫劑利用率高,工程上常用石灰石做脫硫劑。但是,此法有較大的廢水處理問(wèn)題。脫硫廢水水質(zhì)復雜,主要含有懸浮物、硫酸鹽、過(guò)飽和的亞硫酸鹽、以及重金屬等雜質(zhì),很多是國家環(huán)保標準中嚴格要求控制的第一類(lèi)污染物,已成為燃煤電廠(chǎng)最難處理的廢水,是實(shí)現燃煤電廠(chǎng)廢水零排放的關(guān)鍵。面對一直以來(lái)脫硫廢水處理成本高、難度大,傳統脫硫廢水處理技術(shù)工藝操作復雜、效率低下等問(wèn)題,探索有效且經(jīng)濟的脫硫廢水零排放工藝迫在眉睫。
目前國內已有多個(gè)脫硫廢水零排放工程已運行或正在實(shí)施建設。與脫硫廢水零排放工藝相關(guān)的技術(shù)較多,主要包括預處理(除重金屬、硬度等)、膜濃縮減量以及蒸發(fā)結晶、煙道蒸發(fā)、低溫閃蒸、濃液干燥等技術(shù)。通常情況下,采用一種或幾種技術(shù)組合使用,如圖-1所示。
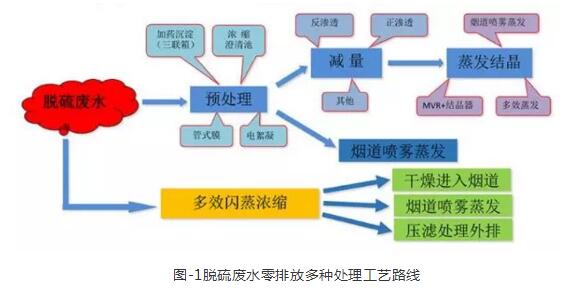
脫硫廢水零排放處理系統主要分為如下三種工藝流程:(1)預處理→膜濃縮→蒸發(fā)結晶工藝;(2)預處理→膜濃縮→煙道蒸發(fā)工藝;(3)低溫閃蒸→濃液干燥工藝。
1.預處理→膜濃縮→蒸發(fā)結晶工藝
工藝流程如下圖:
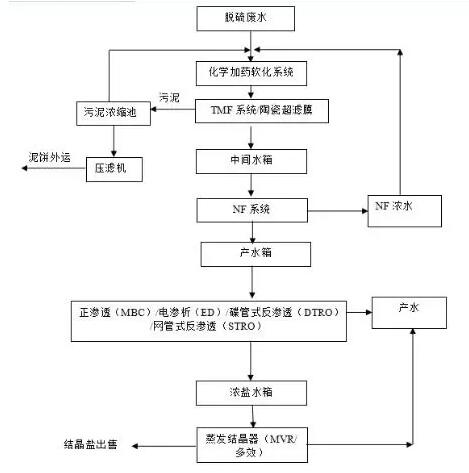
脫硫廢水經(jīng)過(guò)預處理除去重金屬、鈣鎂等結垢離子,出水進(jìn)入管式膜過(guò)濾系統或陶瓷超濾膜去除懸浮物,以滿(mǎn)足后續膜法處理的進(jìn)水要求,采用納濾(NF)分鹽,將納濾濃水返回至預處理系統,納濾產(chǎn)水采用DTRO碟管式反滲透系統或MBC正滲透系統進(jìn)行膜濃縮,以減少后續蒸發(fā)結晶系統的進(jìn)水量,進(jìn)而減少整個(gè)零排放處理系統的投資。蒸發(fā)結晶系統采用MVR或多效蒸發(fā)結晶器,以降低運行能耗。結晶器中產(chǎn)出的鹽主要為NaCL,其純度可大于97.5%,達到工業(yè)鹽干鹽二級標準,結晶鹽可以外售。具體聯(lián)系污水寶或參見(jiàn)http://www.sharpedgetext.com更多相關(guān)技術(shù)文檔。
2.預處理→膜濃縮→煙道蒸發(fā)工藝
工藝流程如下圖:
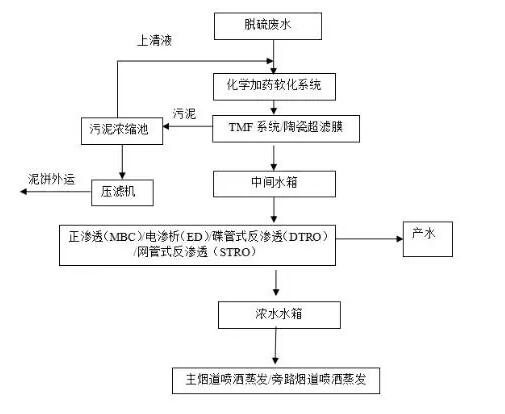
脫硫廢水經(jīng)過(guò)預處理除去重金屬、鈣鎂等結垢離子,經(jīng)過(guò)膜法濃縮減量后進(jìn)入煙道噴灑蒸發(fā)。預處理和膜濃縮系統與上述第一種工藝相似,不同的是,根據濃縮液后處理選擇的方式不同,系統不產(chǎn)生結晶鹽,無(wú)需加納濾進(jìn)行分鹽。
膜濃縮系統的產(chǎn)水直接回收利用,濃縮液進(jìn)行煙道蒸發(fā),利用高溫煙氣將霧化后的廢水液滴蒸干,廢水中的污染物形成細小固體結晶隨煙氣中的灰塵進(jìn)入電除塵器被電極撲捉,進(jìn)入除塵器灰斗外排,從而除去污染物,系統無(wú)結晶鹽的產(chǎn)生,部分水份在脫硫塔中重新凝結被回收利用,最大程度節水節能,達到脫硫廢水的零排放,目前煙道蒸發(fā)工藝主要分為主煙道蒸發(fā)和旁路煙道蒸發(fā)兩種技術(shù)。
3.低溫閃蒸→濃液干燥工藝
工藝流程如下圖:
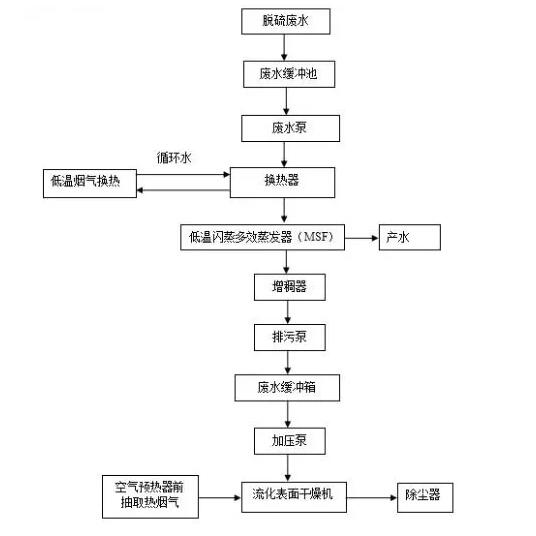
脫硫廢水不需預處理系統,直接利用低溫煙氣的熱量對脫硫廢水進(jìn)行預熱,而后經(jīng)過(guò)多效閃蒸濃縮,濃縮物濃度可在線(xiàn)自動(dòng)可調,濃縮后的濃液進(jìn)入流化表面干燥機蒸發(fā)干燥,產(chǎn)生的粉塵及水蒸氣隨煙氣引入電除塵前煙道,利用電除塵捕捉氯離子和其他固態(tài)顆粒及金屬元素,蒸發(fā)的水蒸汽進(jìn)入脫硫塔。閃蒸濃縮過(guò)程中產(chǎn)生水蒸汽,經(jīng)過(guò)凝結后可回收至脫硫工藝水或其它用途補水。
比較上述不同脫硫廢水零排放工藝,從各工藝的系統配置,優(yōu)缺點(diǎn)以及對熱力系統的影響等方面進(jìn)行說(shuō)明。如下表所示:
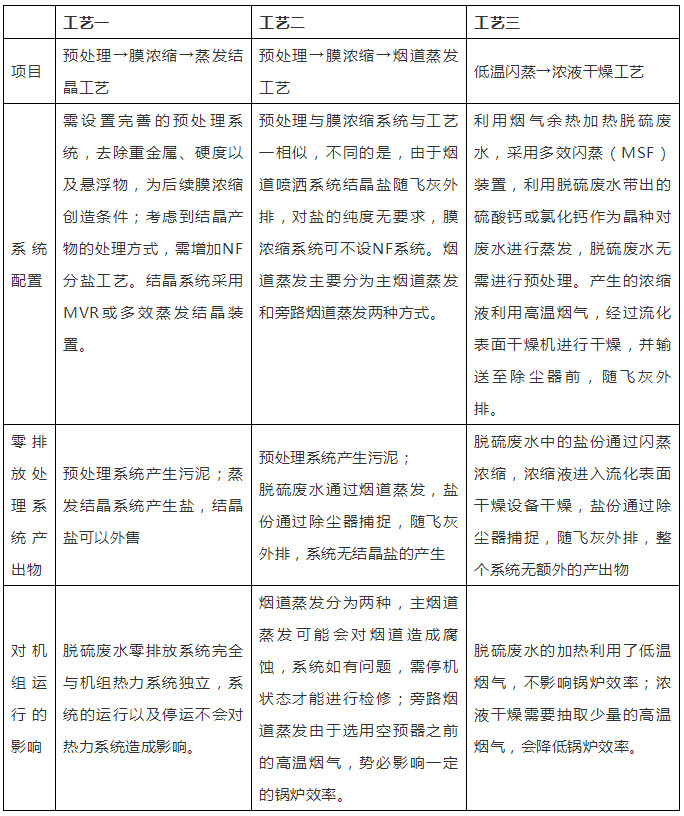
綜上所述,燃煤電廠(chǎng)可以根據實(shí)際運行情況和自身特點(diǎn),選擇適宜的脫硫廢水零排放工藝,對整個(gè)電廠(chǎng)的廢水零排放有著(zhù)至關(guān)重要的意義。(來(lái)源:北極星水處理網(wǎng))