高濃高鹽廢水處理之多效蒸發(fā)技術(shù)
中國污水處理工程網(wǎng) 時(shí)間:2019-3-30 9:16:09
污水處理技術(shù) | 匯聚全球環(huán)保力量,降低企業(yè)治污成本
1.0 引言
隨著(zhù)化工、制藥、造紙等行業(yè)的發(fā)展,高濃度難降解廢水一直是廢水處理的難點(diǎn)。近年來(lái),零排放及污水回用等生產(chǎn)理念的推廣,對污水處理及深度提出進(jìn)一步要求。傳統的物化、生物處理方法處理高濃度難降解廢水時(shí),處理工藝冗長(cháng)且復雜。另外,對于高鹽度廢水,因微生物而不能生存而使生物處理法收到限制,或者需要引進(jìn)大量淡水進(jìn)行吸收達到微生物可以耐受的限制后,采用生物處理。近幾年來(lái),在高濃度及/或高鹽度廢水處理領(lǐng)域,蒸發(fā)技術(shù)開(kāi)始逐漸受到關(guān)注,為長(cháng)久以來(lái)困擾著(zhù)環(huán)保工作者的難題找到了一個(gè)可探索、證實(shí)的答案,并已有一定應用。本文結合筆者工作經(jīng)驗及相關(guān)文獻報道,對蒸發(fā)在工業(yè)廢水處理的發(fā)展及應用做簡(jiǎn)要介紹。
采用蒸發(fā)技術(shù)處理高濃度廢水主要利用水(溶劑)與污染物(溶質(zhì))之間的沸點(diǎn)差異,通過(guò)控制廢水在一定溫度、氣壓下發(fā)生表面或內部的氣化,將溶劑與溶質(zhì)分離的過(guò)程。經(jīng)過(guò)蒸發(fā),沸點(diǎn)高的污染物被留在蒸發(fā)殘液中,而低沸點(diǎn)的水將以冷凝液形式排出。根據蒸發(fā)的原理,只有當污染物與水沸點(diǎn)差異比較大時(shí),才會(huì )有較好的分離效果。否則,污染物會(huì )直接蒸發(fā)成為冷凝液的一部分,或者與水產(chǎn)生共沸而進(jìn)入冷凝液,而導致出水COD升高。因此,對于特定廢水需采用合適的冷凝水處理工藝,使污水處理系統出水達到要求。
目前廢水處理中已有應用的蒸發(fā)設備有多效蒸發(fā)器及機械壓縮蒸發(fā)器。結合筆者的工作,本文就多效蒸發(fā)加以敘述。
2.0 多效蒸發(fā)
2.1 多效蒸發(fā)原理
目前蒸發(fā)器的種類(lèi)很多,就其蒸汽利用角度而言,蒸發(fā)可分為一效至五效。在工業(yè)生產(chǎn)中,為了減少加熱蒸汽消耗量,可采用多效蒸發(fā)。多效蒸發(fā)將多組蒸發(fā)器串聯(lián)起來(lái),除第一效蒸發(fā)采用廠(chǎng)區新鮮蒸汽為熱源,之后的每一效蒸發(fā)利用前一級產(chǎn)生的二次蒸汽為熱源進(jìn)行加熱,因此,多效蒸發(fā)明顯降低了加熱蒸汽的消耗量。另外,除最后一效蒸發(fā)器,每一級蒸發(fā)產(chǎn)生的二次蒸汽在后一級加熱室中作為熱源利用后將成為冷凝水排出,從而大大減少了冷卻水的消耗。
表1多效蒸發(fā)的蒸汽及冷卻水消耗
單效 | 雙效 | 三效 | 四效 | 五效 | |
蒸汽(kg/kg) | 1.1 | 0.57 | 0.4 | 0.3 | 0.27 |
冷卻水(kg/kg) | 13.5 | 6.75 | 4.5 | 3.88 | 2.7 |
由表1看出,隨著(zhù)多效蒸發(fā)級數的增加,處理單位廢水所需的蒸汽量及冷凝水量遞減。然而,隨著(zhù)蒸發(fā)效數的增加公用消耗的減少程度逐漸趨緩,如圖1所示。當蒸發(fā)級數大于三效時(shí),新鮮蒸汽及冷卻水用量的減少量明顯降低。
在設計多效蒸發(fā)器時(shí),不僅需要考慮降低系統能耗,還需考慮設備投資及溫差限制的因素。在廢水處理中,尤其當多效蒸發(fā)系統應用于氯離子含量較高的廢水濃縮時(shí),對設備材質(zhì)的要求會(huì )較高。在需要保證一定使用年限的前提下,對于特定廢水蒸發(fā)設備甚至需要用到鈦材。因此,在采用考慮設計多效蒸發(fā)時(shí),需考慮設備投資的經(jīng)濟性對蒸發(fā)級數的影響。另外,由于裝置總溫差是一定的,各單效的有效溫差比總溫差小很多,從而導致相同總溫差下,多效蒸發(fā)的生產(chǎn)力要低于單效蒸發(fā)器。
相關(guān)文獻表明,在目前廢水處理領(lǐng)域中,三效蒸發(fā)應用較多。
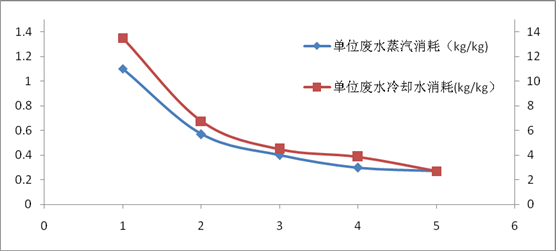
圖1處理單位廢水蒸汽及冷卻水消耗與蒸發(fā)效數的關(guān)系
2.2 多效蒸發(fā)在廢水處理中的應用
在廢水處理中,多效蒸發(fā)被用來(lái)濃縮工業(yè)廢水回收有價(jià)值的成分,或者得到潔凈的冷凝水用以回用。然而在實(shí)際應用中,冷凝水中常帶有低沸點(diǎn)組分的有機污染物,為達標排放通常在多效蒸發(fā)后設計生化工藝來(lái)進(jìn)一步去除水中的有機物。
2.2.1 用于高鹽廢水預處理
筆者在工作中曾參與高含鹽表面活性劑廢水處理的設計。該廢水水量小,CODcr約5000~6000mg/L,TDS含量高達30000mg/L,很顯然微生物很難在該高鹽環(huán)境下正常生長(cháng)。初步論證后,采用蒸發(fā)+生化為主的工藝處理該廢水。蒸發(fā)后幾乎所有鹽分將留在蒸發(fā)濃液中,而大部分冷凝水排出蒸發(fā)系統進(jìn)一步處理后回用。通過(guò)小試發(fā)現,廢水蒸發(fā)濃縮至10%時(shí),冷凝水中的CODcr降至600~800mg/L,濃液TDS含量約30%。在設計過(guò)程中,采用較為經(jīng)濟、節能的三效蒸發(fā)處理原水。蒸發(fā)器的一效、二效采用降膜換熱器,獲得較高的換熱效率,而第三效加熱室則采用強制循環(huán)換熱器,以克服由被加熱介質(zhì)高濃度而引起的設備結垢等問(wèn)題。蒸發(fā)系統的冷凝液經(jīng)換熱后(低于32℃),排入MBR池進(jìn)一步降解,由于進(jìn)入冷凝液中的有機物大多為低分子易降解有機物,MBR出水經(jīng)過(guò)NaCl消毒可達到城市雜用水回用標準。另外,為確保進(jìn)蒸發(fā)系統的SS及CODcr控制在一定范圍內以免設備結垢及傳熱效率受到抑制,在蒸發(fā)前還設置了混凝/絮凝-板框過(guò)濾對蒸發(fā)進(jìn)水進(jìn)行預處理。系統處理流程如圖2所示。
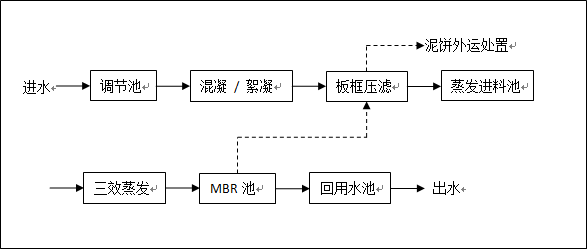
圖2三效蒸發(fā)-生化處理高鹽表面活性劑廢水流程
方麗萍等人采用三效蒸發(fā)+生化的組合工藝處理甲硝唑工業(yè)廢水,出水水質(zhì)達到《污水綜合排放標準》一級排放標準的要求。該工藝首先采用多效蒸發(fā)去除廢水中大部分鹽分和對微生物有毒且難降解的有機物。之后采用氨吹脫去除冷凝水中游離氨,水解酸化+A/O去除有機物。
曹紅等人采用三效蒸發(fā)預處理高含鹽且CODcr高達幾十萬(wàn)的農藥廢水,不僅有效的去除了廢水中的鹽分,還去除了部分有毒難降解CODcr,為后續生化處理奠定基礎。具體聯(lián)系污水寶或參見(jiàn)http://www.sharpedgetext.com更多相關(guān)技術(shù)文檔。
杭州升藍環(huán)保設備科技有限公司在07年就已經(jīng)將三效蒸發(fā)用于高濃度廢水綜合治理。對乙酰氨基酚醫藥生產(chǎn)廢水采用三效蒸發(fā)技術(shù)處理,CODcr去除去率99.95,CODcr由30g/L降低至0.15g/L,對乙酰氨基酚回收率達98%。含鹽量很高的化工染料及中間體生產(chǎn)廢水采用雙相不銹鋼及SS316L為材質(zhì)的三效蒸發(fā)器進(jìn)行濃縮處理,鹽分去除率達98%~99%,出水CODcr在1000mg/L以下,為后續處理創(chuàng )造有利條件。多效蒸發(fā)用于垃圾滲瀝液處理,出水達到排放標準,而成分復雜、毒性高、含鹽量高的母液則采用水泥或瀝青固化處理。
郗金娥等人[10]利用二效蒸發(fā)系統回收醫藥中間體廢水中的鈉鹽。蒸發(fā)出的冷凝水經(jīng)過(guò)臭氧預處理后與洗滌廢水、生活污水混合進(jìn)入厭氧-好氧生化處理系統及后續高級氧化系統,最終出水達標排放。
徐鵬等人[11]采用蒸發(fā)-UASB-SBR工藝處理制藥廢水,當進(jìn)水CODcr、鹽濃度分別為15000~20000mg/L、40~90mg/L,出水達到《化學(xué)合成類(lèi)制藥工業(yè)水污染排放標準》的要求。
2.2.2 用于分離、濃縮或回收無(wú)機鹽
于永輝等人利用四效蒸發(fā)器處理高鹽高硬度稠油廢水,淡水產(chǎn)率為70%時(shí),蒸發(fā)器出水總硬度0.1mg/L,SS為1.1mg/L,油含量0.2mg/L,TDS含量20mg/L,達到熱采鍋爐用水水質(zhì)標準。根據稠油污水特點(diǎn),在多效蒸發(fā)器前設計預處理單元除去污水中的油及懸浮物,防止多效蒸發(fā)器和換熱器污染、堵塞。預處理單元依次為斜板氣浮,核桃殼過(guò)濾器,砂濾器。
鄭賢助等人采用兩效蒸發(fā)回收羧甲基纖維素鈉(CMC)生產(chǎn)廢水中的氯化鈉及羥基乙酸鈉,同時(shí)獲得95%的CODcr去除率。鄭等人采用分步蒸發(fā),分別在兩次蒸發(fā)中回收氯化鈉及羥基乙酸鈉。第一次對氯化鈉的回收效率達到85%,晶體純度較高;第二次蒸發(fā)采用的是第一次蒸發(fā)離心后的鹽母液,回收的羥基乙酸鈉可外賣(mài)提純。
朱壽川報道了還原-中和-沉淀預處理+四效蒸發(fā)工藝處理沉釩廢水,系統出水達到綜合排放標準一級要求。其中,預處理工藝對廢水中六價(jià)鉻及五價(jià)釩的去處理均達98%以上,蒸發(fā)濃縮后的硫酸鹽渣中Na2SO4含量達到70%以上,可作為生產(chǎn)原料。
續京等人對馬鈴薯淀粉廢水進(jìn)行預處理后,采用四效蒸發(fā)回收潔凈的冷凝液用于生產(chǎn)線(xiàn)回用,而母液則作為有機肥處置。
趙斌等人采用三效錯流降膜及蒸汽噴射熱泵的工藝濃縮氯化銨廢水,不僅回收了氯化銨晶體,還從根本上解決了氯化銨工業(yè)廢水對環(huán)境造成的氨氮污染。該蒸發(fā)工藝引進(jìn)了蒸汽噴射式熱泵,利用高壓生蒸汽將一效蒸發(fā)產(chǎn)生的二次蒸汽壓縮后,將低品位的二次蒸汽變?yōu)楦咂肺徽羝麑σ恍д舭l(fā)器進(jìn)行加熱,進(jìn)一步降低系統能耗。
2.3 多效蒸發(fā)系統運行
2.3.1 結垢防治
工業(yè)廢水通常成分復雜,對于高濃度有機廢水更是如此。因此,在利用多效蒸發(fā)處理高濃度有機廢水時(shí)需進(jìn)行預處理,主要需去除水中懸浮物(SS)及浮油。于永輝等人[3]的研究發(fā)現,當多效蒸發(fā)進(jìn)水SS及油含量低于5mg/L時(shí),運行一個(gè)半月后換熱管上沒(méi)有出現明顯污染,而等于5mg/L時(shí),運行72小時(shí)即出現輕微污染。另外,根據水質(zhì)情況,可以在進(jìn)入蒸發(fā)器前投加一定量的阻垢劑以抑制換熱設備表面污染的形成。
筆者工作中多效蒸發(fā)的最后一級換熱器設計為強制循環(huán)式換熱器。多效蒸發(fā)最后一級換熱器中的液體濃度是最高的,此時(shí)溶液晶體容易析出,較易形成垢層。采用強制循環(huán)蒸發(fā)器,在換熱管表面形成較高的液體流速,以減少晶體沉積的概率。
2.3.2 消泡
一些廢水在蒸發(fā)分離室/罐中易起泡而導致蒸發(fā)冷凝水中攜帶較多的污染物。當分離室中的泡沫達到一定高度,泡沫中攜帶的重組分有機物或鹽類(lèi),易被蒸汽帶出分離室而最終進(jìn)入冷凝水中。通常對于起泡的廢水投加消泡劑來(lái)消除泡沫的影響。然而,筆者實(shí)驗過(guò)程中發(fā)現,對于特定廢水,蒸發(fā)過(guò)程中投加酸控制分離室中的廢水pH不小于7,可有效控制起泡。
2.3.4 液膜破裂防治
研究發(fā)現,降膜換熱器內液膜常發(fā)生破裂,尤其已在加熱壁面下部形成趕去并出現結垢(結晶),導致局部溫度急劇上升而過(guò)熱或燒毀,從而限制了降膜蒸發(fā)器在高鹽有機廢水方面的應用。趙賢廣等人研究了降膜蒸發(fā)過(guò)程中液膜破裂的規律,并采用50mg/L的表面活性劑2-乙基己醇,有效控制了液膜的破裂。
2.3.5 能耗
為有效降低蒸發(fā)能耗,楊洛鵬提出了將水平管低溫多效蒸發(fā)技術(shù)應用于廢水處理。通過(guò)將多效水平管降膜蒸發(fā)器和成熟的豎管降膜蒸發(fā)器耦合,能夠在混合式廢水蒸發(fā)器中實(shí)現對熱量的分級利用,廢水蒸發(fā)的能耗得到了大幅度降低。多效水平管降膜蒸發(fā)器增加了廢水蒸發(fā)的投資成本,但在運行費用上具有很大優(yōu)勢。
3 結論
綜上所述,對于高濃度、高含鹽化工廢水,尤其是含有有毒難降解物質(zhì)的工業(yè)廢水,多效蒸發(fā)技術(shù)正在污水處理領(lǐng)域逐漸受到關(guān)注,并可有效應用于生化難以處理的廢水上,或作為生化預處理,與傳統的高濃度有機廢水長(cháng)流程處理系統相比有一定優(yōu)勢。另外,多效蒸發(fā)還可以作為濃縮手段,回收廢水中有價(jià)值的鹽。(來(lái)源:谷騰環(huán)保網(wǎng))